SV861 Non-sagging Road Silicone Joint Sealant
Product Description
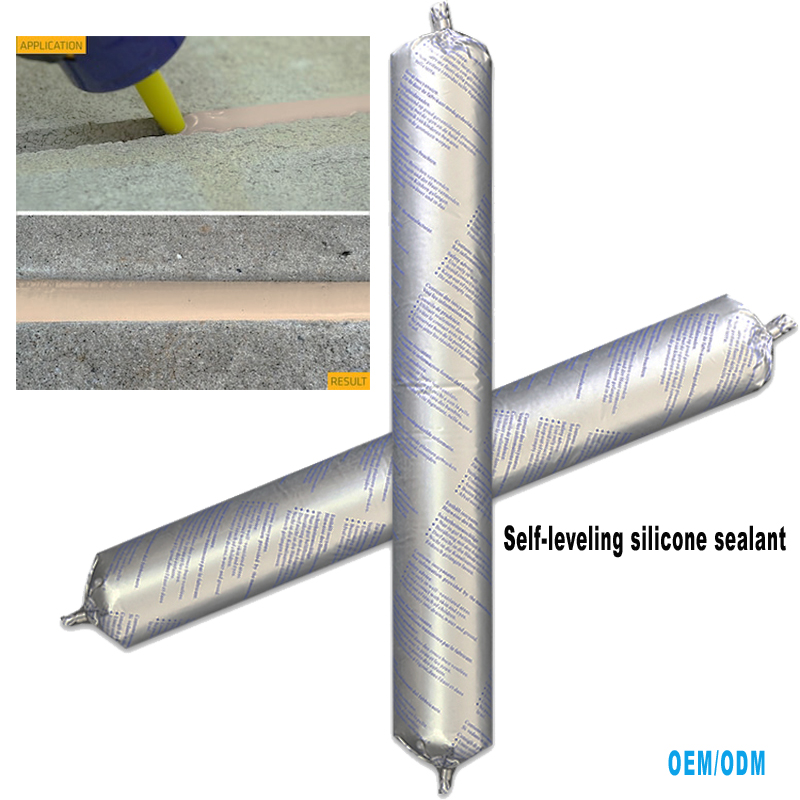
FEATURES
1. Easy to Use: Single-packaged and convenient to use. It has good extrusion application properties within the normal construction temperature range.
2. No Primer Required: Neutral curing, chemically compatible with concrete, and has strong chemical adhesion to concrete. Generally, no primer is needed.
3. Long Service Life: Excellent long-term weather aging resistance, not damaged by sunlight, rain, snow, ultraviolet rays, or ozone. Outstanding high and low temperature resistance. After curing, the formed silicone rubber strip remains elastic at temperatures as low as -40°C without significant hardening or brittleness and does not flow or degrade at +150°C.
4. High Displacement Capacity: Freely follows the expansion, contraction, and shear deformation of concrete joints without being damaged.
5. Low Modulus: Produces moderate low stress on the concrete substrate during passive deformation, ensuring that the concrete surface layer is not damaged.
6. High Elasticity and High Recovery Ability: Can repeatedly follow joint movement, with fast response and recovery and low permanent deformation.
MOQ:1000 Pieces
PACKAGING
Composite soft film packaging, net capacity 590ml.
For other packaging options, please call for consultation.
COLOURS
gray or other colors as required by the user.
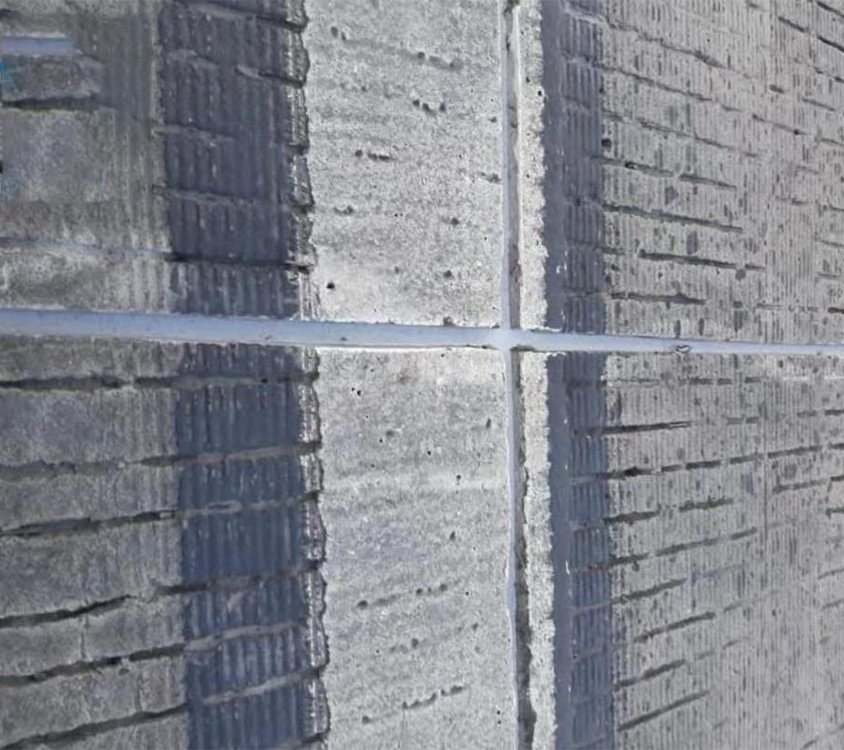
Applications
1. Used for joint sealing of airport runways and highways, capable of withstanding large displacements.
2. Used for joint sealing of other concrete pavements.
3. Used for sealing in subway projects, tunnels, bridges, and other projects.
4. Used for joint filling and sealing of ballastless tracks.
Typical Properties
These values are not intended for use in preparing specifications
Performance |
Index |
Measured Value |
Test Method |
|
Sagging | Vertical, mm | ≤3 | 0 | GB/T 13477 |
Horizontal | No deformation | No deformation | ||
Extrudability, ml/min | ≥80 | 487 | ||
Skin Drying Time, h | ≤3 | 1.0 | ||
Elastic Recovery Rate, % | ≥70 | 85 | JC/T 976 | |
Tensile Modulus / MPa | 23°C | ≤0.4 | 0.35 | |
-20°C | ≤0.6 | / | ||
Set Extension Adhesion | No damage | No damage | ||
Adhesion after Hot Pressing and Cold Pulling | No damage | No damage | ||
Set Extension Adhesion after Immersion | No damage | No damage | ||
Set Extension Adhesion after Heat Treatment | No damage | No damage | ||
Hardness Change after Heat Treatment, HsA | ≤10 | 3 | ||
Thermal Aging | Thermal Weight Loss, % | ≤8 | 4 | GB 16776 |
Cracking | None | None | ||
Chalking | None | None |
Product Information
Usage Limitations
- Not suitable for construction in adverse weather conditions.
- Not suitable for use on frosted or wet surfaces.
- Not suitable for all materials that exude grease, plasticizers, or solvents, such as the surface of oil-impregnated wood.
- Not suitable for continuously immersed water or oil areas.
- Not suitable for use in poorly ventilated places, as the sealant needs to absorb moisture from the air for curing.
- Not suitable for construction when the surface temperature of the material is lower than 4°C or higher than 40°C.
- Newly poured concrete should be cured in dry weather for at least 7 days. In case of rain, one additional dry day is required for each rainy day to ensure at least 7 days of dry curing. For projects that need to be completed quickly or for fast-drying types of concrete, please contact the technical service personnel of Siway Chemical.
- When installing the sealant, it should be lower than the road surface to prevent wear.
- Substrate Usage Limitations: Not suitable for use on copper, lead, galvanized metal surfaces, and polycarbonate materials.
Technical Services
Provide complete product technical information.
Adhesion Testing:
SV861 silicone road sealant has excellent adhesion to concrete and generally does not require primer treatment. However, due to the diversity of concrete formulations and different surface cleaning conditions, we cannot guarantee that the sealant is suitable for all road concretes. Small-scale adhesion tests on the construction site must be carried out before large-scale use to develop a reasonable plan to ensure good adhesion.
Construction Methods:
(1) Interface Cleaning
a) Cutting (for new interfaces) or joint cleaning (for old interfaces):
i. Cutting: After the concrete is completely cured and before applying the sealant, the interface should be cut twice to make the width and depth of the joint meet the design requirements.
ii. Joint Cleaning: Remove all the old sealant materials remaining in the interface. For old sealant materials that are difficult to remove, solvents, sandblasting, or mechanical grinding can be used. If the old sealant cannot be completely removed by the above methods, the interface should be cut wider. If the old interface uses silicone sealant, first check the adhesion between the colloid and the interface surface. If the adhesion is good, a thin layer of glue can be left on the interface surface. When using the same type of silicone sealant, the old and new colloids will naturally combine into one body without affecting the adhesion and sealing performance.
b) High-pressure Water Column Cleaning: Use a high-pressure water column to wash out the impurities remaining in the interface.
c) Drying: Let the interface dry naturally.
d) Sandblasting Cleaning: After the concrete interface surface is dry and before applying the sealant, reconfirm whether the interface surface is clean and firm. You can touch the interface surface with your fingers. If there is still powder or other substances attached, it means the interface surface has not reached the firm effect. A sandblaster should be used to blast the interface surface until no powder flakes off. Sandblasting can also increase the bonding area of the groove wall and improve the bonding performance between the glue and the substrate.
e) High-pressure Air Blowing: Use high-pressure air of at least 90psi (0.62MPa) without oil and water vapor to blow the fine sand and other impurities out of the interface.
(2) Installation of Backing Material: After the interface cleaning is completed, the backing material and the sealant should be installed as soon as possible. If the backing material is not installed immediately after cleaning, it is recommended to repeat the high-pressure air blowing step before installing the backing material. The backing material should be wider than the interface. The installation recommendations for the backing material (for shallow interfaces) are shown in Table 1.
Table 1 Installation Recommendations for Backing Material (for Shallow Interfaces), unit: mm
Interface Width |
6 |
9 |
13 |
19 |
25 |
Depression Depth |
9 |
9 |
9 |
9 |
9 - 13 |
Sealant Thickness |
6 |
6 |
6 |
9 |
13 |
Spacer Rod Diameter |
9 |
13 |
16 |
22 |
32 |
Total Interface Depth |
25 - 29 |
29 - 32 |
32 - 35 |
41 - 44 |
57 - 60 |
(3) Application of Primer Solution: For a very small number of substrates, a primer solution may sometimes be necessary to enhance the adhesion between the colloid and the interface surface. The primer solution should follow the recommendations and processes of the sealant manufacturer.
(4) Applying the Sealant:
a) Insert the nozzle of the sealant deep into the interface to ensure that the sealant can fill the entire interface from the bottom up without air bubbles getting trapped inside.
b) Push the nozzle of the sealant into the interface at a 45° angle instead of dragging it.
c) For an interface of a certain length, apply the sealant steadily and continuously. Try to avoid inconsistent application speeds, which may cause too much or too little sealant in the interface.
d) Control the construction speed by adjusting the pressure of the sealant gun, the size, and shape of the nozzle.
e) Use an appropriate trimming tool to squeeze and level the sealant surface from top to bottom, ensuring that the sealant is in full contact and bonded to the interface surface under pressure.
f) After applying the sealant, check the joint filling situation to ensure that there are no problems such as lack of sealant, blistering, or bulging. If any problems are found, deal with them immediately.
Contact Us
Shanghai Siway Curtain Material Co.Ltd
No.1 Puhui Road ,Songjiang Dist,Shanghai,CHINA Tel: +86 21 37682288
Fax:+86 21 37682288